Lean Manufacturing: Optimizing Efficiency and Eliminating Waste
- saharsh D
- May 22, 2023
- 3 min read
In today's competitive business landscape, organizations are constantly striving to improve operational efficiency, reduce costs, and deliver high-quality products and services to their customers. One methodology that has gained significant traction in achieving these goals is Lean Manufacturing. Lean principles focus on eliminating waste, improving processes, and maximizing value, leading to enhanced productivity and customer satisfaction.
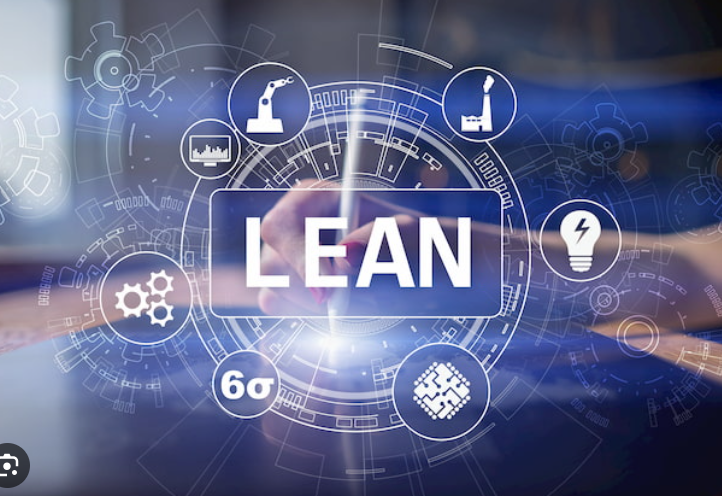
In this blog, we will explore the core principles of Lean Manufacturing and how they can optimize efficiency and eliminate waste in various industries.
1. Understanding Lean Manufacturing
Lean Manufacturing is a systematic approach to process improvement that originated from the Toyota Production System (TPS) in the 1950s. It emphasizes the elimination of non-value-added activities, known as waste, in all aspects of the production process. Waste can manifest in different forms, including overproduction, excess inventory, defects, waiting time, unnecessary movement, and underutilized talent. By identifying and eliminating these wasteful practices, organizations can streamline operations, reduce costs, and improve customer satisfaction.
2. The Five Principles of Lean Manufacturing :
a. Identify Value: The first step in Lean Manufacturing is understanding what the customer considers as value. Organizations must align their processes to deliver products or services that meet customer needs while eliminating activities that do not contribute to value creation.
b. Map the Value Stream: Value stream mapping involves analyzing the entire flow of materials, information, and processes required to deliver the product or service. By visualizing the value stream, organizations can identify bottlenecks, redundancies, and opportunities for improvement.
c. Create Flow: Once the value stream is mapped, organizations must strive to create a smooth and uninterrupted flow of work. This involves removing obstacles, minimizing handoffs, reducing cycle times, and ensuring a continuous flow of materials and information.
d. Establish Pull: The concept of pull refers to producing or delivering products or services based on customer demand. By adopting a pull system, organizations can avoid overproduction, reduce inventory levels, and respond quickly to changing customer needs.
e. Pursue Perfection: Lean Manufacturing is a continuous improvement philosophy. Organizations must constantly seek perfection by setting high standards, measuring performance, identifying areas for improvement, and implementing solutions. This involves empowering employees to participate in problem-solving and fostering a culture of continuous learning and innovation.

3. Benefits of Lean Manufacturing
Implementing Lean Manufacturing principles can bring numerous benefits to organizations, including:
a. Increased Efficiency: By eliminating waste, streamlining processes, and improving flow, organizations can significantly enhance operational efficiency. This leads to reduced lead times, improved productivity, and increased capacity to meet customer demands.
b. Cost Reduction: Lean Manufacturing eliminates unnecessary activities, reduces inventory, minimizes rework and defects, and optimizes resource utilization. These actions result in cost savings, improved profitability, and a competitive advantage in the market.
c. Enhanced Quality: By focusing on process improvement and defect prevention, Lean Manufacturing helps organizations deliver higher-quality products and services. This leads to improved customer satisfaction, increased customer loyalty, and a stronger brand reputation.
d. Employee Engagement: Lean Manufacturing encourages employee involvement in problem-solving, decision-making, and process improvement. This promotes a culture of continuous learning, empowerment, and engagement, leading to increased job satisfaction and retention.
e. Flexibility and Adaptability: Lean Manufacturing enables organizations to respond quickly to changing customer demands, market trends, and unforeseen disruptions. The emphasis on flow, pull systems, and continuous improvement allows for greater flexibility and adaptability in operations.
4. Implementation Challenges :
While the benefits of Lean Manufacturing are significant, implementing the principles can present challenges for organizations. Some common obstacles include resistance to change, lack of employee buy-in, inadequate training, insufficient resources, and difficulty in sustaining the gains achieved through Lean initiatives. Overcoming these challenges requires strong leadership and commitment from all levels of the organization, effective communication and training programs, and a long-term dedication to the principles of Lean Manufacturing.
Conclusion:
In conclusion, Lean Manufacturing is a powerful methodology that enables organizations to optimize efficiency, eliminate waste, and deliver value to customers. By understanding the five principles of Lean Manufacturing and implementing them effectively, organizations can streamline processes, reduce costs, improve quality, and enhance customer satisfaction. The benefits of Lean Manufacturing extend beyond operational improvements, as it also fosters employee engagement, promotes a culture of continuous improvement, and enables organizations to adapt to changing market demands.
References:
Every manufacturing unit must implement Lean manufacturing. Excellent content !